2014年11月21日(金)に星陵會舘ホール(東京都千代田区永田町)で、第7回品質工学技術戦略研究発表大会(以下、RQES)が開催された。品質工学は「社会的自由の総和の拡大」を基本理念とし、世の中のロスをコスト換算したとき、そのコストが最小となることをめざしている。その手段として、パラメータ設計による技術の頑強(ロバスト)性向上、損失関数の生産工程への適用、MTシステムと呼ばれる多次元データを用いた予測・診断・判定技術、直交表のソフトウェア評価への適用がある。ここ数年、品質工学会でいわれていることは、それら個々の手段の研究だけではその効果は不十分であり、技術開発のマネジメントとうまく同調し、戦略的に技術開発を進めるということである。
大会開催にあたり、品質工学会会長である齊藤潔は開会あいさつとして、「技術戦略大会とは何か、品質工学とは何かを考えるための議論をする場としてRQESは設定されている。近年の学会としての方向性はマクロ視点である。また、技術戦略ではテーマの決定が極めて重要である。そこで、サブテーマは『マクロ視点からの戦略的評価基準の決定』とした。戦略的評価基準とはさまざまなテーマにおいて共通する内容である。最近、技術者がミクロな視点になっているのではないかと危機感がある」と述べた。
筆者は、昨年のRQES2013のまとめとして「同じゴールをめざしたそれぞれの立場の人が、各々考えながら仕事をしているはずなのに、必ずしも有機的に作用しないことがある。それは、曖昧なゴール設定のせいであろうか、プロジェクトを横断的に見る機能が有効に働いていないからだろうか。他にも要因はあるがそれらの多くはマネジメントの問題である。マクロ視点で捉える必要がある巨大システムの最適化では、なおさらマネジメントの問題が重要と考えられるため、適切なテーマ選定、目的の明確化と共有化、具体的かつ合理的な実行手段の何れかが不十分ではマクロ視点でのシステム最適化は成し得ない」と記した。少しずつ定着してきた感のあるマクロ視点であるが、今年の議論でさらに広い視点で技術開発のマネジメントをさらに促進させるヒントが得られるか着目した。
研究発表1「工業標準における標準設定方法の研究(応用計測研究所(株)、矢野宏)
サブタイトルは「技術者としての自立の道を探る」である。矢野は通産省計量研究所において工業標準の標準設定に携わり、技術者としてどう自立してきたかわかったという内容であった。矢野がおこなった大きな仕事は、硬さ標準の設定、プラスチック寸法測定の研究、標準ガスの設定である。公的機関で標準を作る研究をしても、研究をすれば企業にすぐ標準を採用してもらえるというものではなかった。企業に標準を役立ててもらうという目的が容易に達成できなかったのである。普通の感覚としては、よりよい標準ができたのなら使えばいいではないかと考えるが、実情はそう簡単なものではないようであった。それは、技術の世界にも存在する既得権益による「しがらみ」のせいである。米国のアナリストであり経済学博士のロバート・フェルドマンによると、「技術監督体制が技術環境と離れてしまうと、監督制度が古い産業構造のままであるが故のずれが生じる。その時、既得権益を譲りたくない『しがらみ』が発生する」そうである。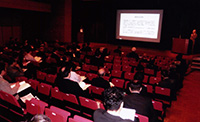
矢野は研究の成立として、(1)研究プロジェクトの立ち上げ、(2)研究の本体、(3)研究の成果を生かすことがあるとしている。一般に(2)の研究が重視されがちで、(3)の研究成果を生かす部分、すなわち目的達成までが弱い。これは、標準がすぐに採用されなかったことに関連する。科学史家の中山茂によれば「日本人には個人として優れた技術者が多いが、研究計画の調整ができていない。有効な成果を引き出しにくい」とのことである。研究計画の調整はマネジャーの仕事であるので、マネジメント力の欠如により成果が成果にならない事態を生じさせている。
また、技術とは本来アートであり、しかも個人だけでは成すことが難しいため、集団によるアートとなる。よって技術のマネジメントは集団による芸術の創造であり、研究の側面で技術者にこの意識が必要とのことである。矢野はこの意識があったかという自問を通じて、自身の技術者としての振り返りをしている。その結果、(1)戦後体験から無意識の働きにあった合理性の追求、(2)有効な技術を作ろうという意志はあった、(3)国立の研究所が公的意識を育てた、(4)同時に良いメンバーに恵まれた、(5)外部企業などの優れた技術者の支えがあった、という5つが述べられている。どのような技術者であっても、この5項目と同等な資質と条件は必要なのではないかと考える。しかし、企業に属する技術者には(3)の公的意識と(5)の外部とのつながりが欠落しがちではないだろうか。品質工学の基本理念である「社会的自由の総和の拡大」は公的意識と結びつくものがあり、学会のコミュニティーにおける他業種の技術者との関わりは、まさに外部とのつながりであるといえる。
パレート図で有名なV・パレートは、「自分の感情を行動で外に向かって表現したがる傾向」を人間の基本要素の1つとしているが、それに関連し経済学者の森嶋通夫は、教育の歴史的な役割を重視した。歴史社会学者の大淀昇一の著作『技術官僚の政治参画−日本の科学技術行政の幕開き』(中公新書、1997)によると、1878(明治11)年に制定された自由主義的教育令で、「高等教育を受けようとする青年は『法科政学』を学ぶのはごく少数の優秀な者のみに限る。あとの大部分は『科学』や『工芸技術百科ノ学』を学ぶ方向に導くべし」「科学技術についての学習が盛んになれば、政治に関心を持つ若者はおのずと少なくなる」との記述を指摘している。この制定により、技術者は社会的に閉じ込めにあったと言う。われわれ技術者が自由と言っているのは、技術者を排除した政治によって作られた殻のなかでの自由に過ぎない。
サブタイトルにもある自立とは本来独力で物事をおこなうことであるが、技術は集団のアートであるなら集団で物事をおこなえるようになることが、矢野のいう技術者としての自立と考えても強ち間違いではないだろう。矢野は、技術者個人として「しがらみ」を断ち切ろうとする組織のなかの個人的な意欲が重要としている。個々の技術者が自分で物を考え、集団のアートとしての技術を完結して成果をアピールする必要がある。技術開発のマネジメントの1要素である技術者に焦点を当てた研究内容であり、筆者にとって技術者の端くれとしての自分のあり方を考えさせる発表であった。
研究発表2「硬さ標準統一の闘いとベアリングの硬さの損失関数」((株)アサヒ技研、中井功)
矢野と共におこなった硬さ標準設定の研究課程を振り返り、既得権益に対する課題とベアリングの硬さに損失関数を適用し、目に見えない損失の受け入れられ方を検討した。研究発表1のさらに具体的な内容といえる。
1960年代の日本の代表的な輸出品は、ベアリング、時計、カメラであった。ベアリングの機械的な材料特性として広く利用されているロックウェルCスケール硬さにおいて、校正用の硬さ基準がどのように決定されているか不明であった。当時、地方公設試験研究機関の基準は10HRC近くの差があったとのことである。各社の基準値に相違があるにもかかわらず、各社共に規格値の範囲にあると主張していた。そのような状況であったため、日本ベアリング協会は権威のある基準を必要とし、東京大学と計量研究所に基準の作成を依頼した。これが権威と利害の闘いの始まりであった。もし基準とする値と差がある基準を使用しているならば企業は、基準を変える対応が要求されるからである。社会全体としてではなく自社のみの損得勘定が働いたのである。
1960年頃に計量研究所がロックウェルCスケール硬さ標準の設定に成功し、国鉄技術研究所により新幹線のベアリングの硬さ規格として採用された。中井がいた日本軸受検査協会(JBI)の硬さ統一委員会でも、この硬さ標準を採用することを決定した。ベアリングメーカーは、新幹線用ベアリングについては新標準を採用したが、それ以外は自社の従来の基準を守ろうとしたため、利害が入り乱れた。中井は、正しい標準が企業の利害により採用されない矛盾に気がつき、新しい標準による統一をはかることにした。これがタイトルに記された闘いの始まりである。
1970年頃に通産省が生産量の少ないベアリングの型番について国際競争力を維持するため、各社に特定の型番のベアリングの生産を割り当てる共同生産方式を採用した。そのとき、自社品と他社品で硬さ基準片が異なるという異常な状況となったが、ベアリングメーカー各社が目先の利害を優先して、硬さの基準に違いがあっても各社規格値を満足していると主張した。正しく校正できないことによる、目に見えない損失があるはずだが認識されなかった。これは規格内であれば問題ないという思想の表れであった。
そこで、JBIが統一された硬さ基準を持つよう要望された。研究発表1で記したとおり、計量研究所も硬さ標準を設定したが普及がうまくいっていなかった。そこで計量研究所とJBIの共通課題として硬さ標準の普及をおこなうことになった。硬さ標準の普及にあたり、大手ベアリングメーカーを訪問して説得したが、各社から強い抵抗を受けたそうである。またJBI上層部からもサポートが弱く、標準統一への歩みは遅かった。これはマネジメントの協力が得られず物事が進まないという状態で、今でもどこでも散見されることである。さて、弱小組織のJBIが大手ベアリングメーカーに立ち向かうには、硬さ標準を活用した硬さ試験機の校正のあるべき姿を示す必要があった。ちょうどその頃「産業計測標準委員会」が組織されていて、そのなかに「硬さ技術基準作成小委員会」が組織され、検討の末、「硬さ標準トレーサビリティシステム」が完成した。
また、使用中の誤差を管理することによって信頼性を高めることで、硬さ標準の本来の意味でのトレーサビリティが実現できるとの考えのもと、JBIは計量研究所と「硬さ標準のトレーサビリティを評価する基準に関する研究」をおこなった。その1つとして、最適校正周期による管理システムとベアリングメーカーが採用していた管理システムを比較する経済性評価をおこなった。その結果、最適校正周期による管理システムはベアリングメーカーの校正方式より2〜6割の損失低減という結果となり、硬さ管理方式の合理性を示した。しかし、ベアリングメーカーにほとんど理解されなかった。品質工学が提唱する「損失関数」は目に見えない損失であるが故にその検証が難しく、その部分をどう理解させるかが品質工学における大きな課題である。
研究発表1にあったように、オーソライズされた信頼性の高い硬さ標準ができても、何らかの強制力を持たなければ使用されるとは限らない。ベアリングメーカー各社は現状では困っていないから標準を変えたくない、いいかえれば「検査に合格すればよい」という思想であった。結局のところ、中井はこの思想そのものを変えるには力が及ばなかった。しかし、最終的に10年の歳月を費やし、標準の統一は実現した。技術が進展しても法律や既存の規格などが追従できないことや、従来からの慣習の違いによる制約から研究成果が生かされないという問題は、いつの時代でも企業内外を問わずみられる。このような状況を回避するために、研究活動を開始する際に、研究成果の活用を同時に考えたプロジェクトを立ち上げる必要があることを示唆している。
会場からの「統一を実現することは魅力的かつ独創的な研究である」という意見に対し、中井は「1955(昭和30)年代、硬さ標準作りは魅力であったが、すぐにはできなかった。魅力を維持することが大切。自分たちで1から作ることは難しい」と答えた。「技術者の成果をどう社会に活かすかという点が疎い。品質工学会もエコシステムを考え、社会に活かさなくてはならない」という点に対しては、「1回の研究ではなく、研究が続くことが必要」と述べた。
たとえ良い研究であっても、技術者の思いだけでは研究成果が活かされないということもありうる。これは研究を統括するマネジメントの問題であろう。中井の場合は所属組織のサポートが得られにくい状況であり、同じ目的を持った計量研究所とで支えあって、個人の意地にも近い努力で何とか成果を活用に漕ぎつけた感じである。品質工学の活用が進まない企業についても、個人が草の根レベルで活動している話をよく耳にする。上意下達で動くのが組織であるから、マネジメントが理解しなければ何事も進展は遅くなる。また複数の組織が関係するときのマネジメントをどうするかが難しいと感じた。
研究発表3「損失関数を活用した大規模オフィスビルの防災備蓄の検討」(富士ゼロックス(株)、曽我光英)
テーマ設定で大切なことは、品質工学の創始者である田口玄一の提案「統計の役割」、今でいえば「品質工学の役割」である次の3項目に集約されている。(1)社会問題の発生予測や診断自体が必要のない社会にする、(2)前述が不可能か不経済のとき、安くて誤りの少ない予測・診断・判定の方法を考える、(3)さらに前述がうまくいかない場合、誤りが起こっても損失が最小になる処置を考える。
日本は自然災害の多い国で、毎年概ね数千億円、東日本大震災が発生した2011年は6兆4000億円の損失によるコストが発生している。特に地震による被害が突出しているということである。また、東日本大震災では交通網が麻痺し、いわゆる帰宅困難者が大量に発生した。東京都は帰宅困難者対策として、事業主に対し3日分の水・食料・その他必要物資の備蓄の努力義務を課すという条例を施行した。そのような背景のもと、曽我は勤務するオフィスビルの備蓄の検討を(2)に該当するテーマとして設定し、損失関数を適用した研究内容を報告した。検討する前提として、従業員が最も多い時間帯に地震が発生し、従業員を3日間事業所内に留めておくという状況を想定した。3日間の根拠は、一般に72時間が生死の分かれ目ということによる。また3日間、十分に水分や食料が摂取できない状態で従業員の健康に悪い影響を与えることが品質問題とした。損失関数を用い品質問題を可視化するにあたり、機能限界時の損失A0を国民所得×平均余命とし、機能限界Δ0を水分が取れずに死亡する場合と、食料が取れずに死亡する場合の2項からなる損失関数とした。
備蓄の問題も、コロンビア大ビジネススクール教授のシーナ・アイエンガー「選択の科学」にあるように選択の問題であり痛みをともなうものであるという。選択の意思決定は「現時点で眼に見える損失」と「将来発生するかどうか不確実な危機についての目に見えない損失」のバランスで決まるため、両者をどう選択するか合理的に検討する必要がある。次に選択問題を「受け入れられるリスク」と「受け入れられないリスク」として捉えていたが、リスクアセスメント的な考え方だと感じた。リスクアセスメントは個々の事象の重篤度×発生頻度でリスクの重大性を計算する。つまり「受け入れられるリスク」になるか「受け入れられないリスク」になるかは、個別の事象のリスクの程度だけで決まるものではなく、その発生確率と一緒に考えることになる。たとえば、個別で見れば無視できるようなことでも、たびたび発生するなら無視できなくなる。曽我はリスクアセスメントでは「受け入れられないリスク」と判断されることを如何に受け入れさせるかとして、「リスク低減係数R=備蓄がない時の損失/備蓄コスト」という指標を提案した。リスク低減係数Rが大きいほど優先的にそのリスク低減策に取り組むというものである。たとえば、今回の事例では食料よりも水を優先させて備蓄すべきという選択となる。
東京都により、条例施行後約1年が経過した。実態把握のアンケートによると飲料水の備蓄3日以上の事業所が約5割に達しているが、備蓄への取り組みばらつきが大きい。事業主の備蓄あり・なしの「選択」に関し、選択の科学にある「自動システム」と「熟慮システム」という2つの脳回路を使って情報処理し回答を出すということに着目した。スペース問題や初期投資問題は想起しやすく、自動システムによって備蓄しないという判断に陥る。自動システムを超えて、熟慮システムに判断を移行させなければ、課題とすら認識されない。そうなると「確認バイアス」が働き、備蓄しない選択を正当化するような情報のみ進んで受け入れ、備蓄しないという判断結果をなかなか変更できなくなるということにある。
損失関数はリスクではなく、リスクが発生したときのコストである。しかし、一般に確率を考慮したリスクで判断する傾向があるようである。そこに損失関数の普及につながらない理由があるように感じた。損失関数の活用例がいろいろ出てくることは、一般の理解を高める意味でよい。コスト換算をすることが、実施したテーマの企業や社会への貢献度を定量的に示す最も直接的な方法である。損失関数は技術開発のアウトプットをコスト化し、コストという経営指標へとつなげる役割を果たすが、損失関数は目先の利益ではないため、なかなか有効利用されない。損失関数は誤差分散2σに損失が比例するというとても単純な式であるが、いまひとつ活用が進まない。損失関数で求められる損失は未然防止できるロスコストであり、将来自企業が被らなくて済む損失なので実感が沸かないのである。つまり、ほとんどの人は目先のことを理解するのに精一杯なのである。研究発表2で、プロジェクト立ち上げ時に研究成果の活用を同時に考えるということも、将来のことを今のことのように理解するということであり、本研究は話としてはつながると感じた。「将来の予測」は品質工学のキーワードの1つである。
研究発表4「技術展開の実践マネジメントにおける機能性評価基準−品質工学誌の論文から推測する技略の展開の具体化−」(クオリティ・ディープ・スマーツ(有組)、吉澤正孝)
技術展開(技展)とはマネジメントのオペレーションであり、その目的は開発された汎用技術(技略=技術戦略)を組織的に商品・サービスの開発あるいは生産、製造工程に適用して事業の成果を出すためのその運用のことである。また、その過程で品質工学を研究・開発することでもある。技展に関し、人材育成・開発と技術フォーカスについて研究し、昨年度は、吉澤が過去に所属していた複写機業界からの発表論文を1つの手がかりに、新製品開発への品質工学の組織的展開を検討し、実践のマネジメントについて明らかにした。そこから商品開発における品質工学の適用の方向性とマネジメントとしての評価基準が得られたがマネジメントのテーマ選択に対する指針に対する検討は不十分であったため、今回テーマ選択について研究をした。
テーマ選択において、マネジメントとしておこなわれなくてはならないことは、(1)経営戦略や組織の戦略目標を達成するための新規開発テーマを選択する、(2)テーマをサブプログラムに分解し全体とサブプログラムの評価尺度を決めるである。今回の研究は(1)についてテーマ選択とマネジメント機能およびその評価について方向性を検討するものであった。その検討方法として、(1)10年以上品質工学を実践している組織、(2)マネジメント層が論説、論文を発表している組織、(3)現在も品質工学会で発表がされている組織に該当する5社を選定し、論文や研究発表からテーマ選定に関する分析を実施した。
長期的な観点でのテーマ選択の検討として、田口から実験計画法を学び始めてから42年活用している企業である富士ゼロックス社を調べた。富士ゼロックス社の品質経営レベルの狙いは、 (1)市場ニーズに合致した新製品の早期開発、(2)徹底した重点思考による営業力強化、(3)源流にさかのぼり全社一丸となったコスト合理化、(4)新しい基礎技術の積極的導入と設定されていた。また、これらを運動の目標としたNX運動を旗揚げした。このこと自身が一種のテーマ選択というのが吉澤の解釈である。経営陣はNX運動という経営方針として、組織改革の狙いが明確にされた中長期計画の1つのタスクあるいはプロジェクトとして品質工学を選択した。吉澤は5社の経営における戦略課題を調べ、仮説として、大規模企業では組織全体を1つの旗の元に集約することは、組織内への展開効率を上げる1つの方法であるとしている。また、このように大きな活動が完結したあと、継続を目的とした活動をどうするかのパターンは、(1)トップマネジメントレベルでの引き継ぎ、(2)部門の戦略案件から出てくる戦略的手段を技術化・技闘化する活動、(3)新たに方針を設定しても展開・実践が継続されるということである。
次に品質工学適用過程の各フェーズ、(1)導入初期、(2)品質工学の効果検証後、(3)新製品開発プロジェクト、(4)各機能組織独自の展開におけるテーマ選択について検討した結果、テーマ選択は以下のようにするのがよいと提案された。(1)では、田口がベル研でしたように、最も重要な技術問題は何かを問う。(2)では、各組織における重要品質問題、新製品開発プロジェクト、新製品や製造工程の目的を開発する前に研究・技術開発テーマを選択するのがよい。(3)では、最も重要な製品に適用、同時期開発される全商品開発に適用、理想は全商品開発であるが、状況に応じて複数の製品開発に適用する。(4)では、品質ロスが多いラインからテーマ選択、手戻りの多い生産準備、絶対原価から乖離したラインからテーマを選択することである。
マネジメントとしてのテーマ選択は単純ではなく、一貫性と整合性が必要とされる「テーマ選択の三階層」を成している。それは、(1)上位層:組織の改革、革新などの経営戦略課題、(2)中間層:組織改革、革新などを遂行するための重点となる商品、ライン、技術など、(3)下位層:選択した重点商品、ライン、技術などであり、そこからマネジメントとして重要な課題をテーマとする。これはマネジメントの方針展開の連鎖である。方針の展開の中に品質工学を位置づけて、それにより成果を出すことは、マネジメントそのものを実行することになる。しかし、組織的効果を出すには十年〜数十年の単位を必要とする。それは、品質工学に取り組む技術者や経営者に対し、設計技術の根本的なところから変革を要求するからである。また、これらの組織的展開は、技術者などのボトムの責務ではなくマネジメントの責務である。品質工学の本質である田口が主張した技術開発の考え方の本質を上位マネジメント層が理解しておく必要がある。
会場からは「アルプス電気の取り組みである“一発完動”のような高い目標を与えるのは品質工学から見たらどうか」という質問に対し、「マネジメントが目的で品質工学はその手段。一発完動は理想機能ではないかと思う。マツダはSKYACTIVEエンジン開発で、役員皆でエンジンのあるべき姿を議論した」、「マツダには絶対原価という言葉がある。あるべき姿である。目標は会社の上位に行くほど具体的でなくてもよい。しがらみに縛られない」という意見があった。また、一発完動の仕掛け人であるアルプス電気の谷本からは「品質工学はマネジメントの技法だと考えている。今の世のなかで、先を読んで技術をマネジメントできるのは品質工学である。一発完動を言ったのは、やってみてダメなら直すことから脱却したかったからである。マネジメントが本質の考えを学習することが大切。そこがわかれば、後はスタッフに任せればよい」とのコメントがあった。
技術開発のマネジメントのうちテーマ選定について、吉澤らしい研究内容が報告された。マネジメントが品質工学の有用性を理解して旗を振っている場合は有用な情報であるが、多くの企業ではマネジメントにどうやったら旗を振ってもらえるかで困っている。現実は「テーマ選択の三階層」の下に問題解決という第4の階層があり、そういう人たちは、その最下層のテーマ選択しかできずにもがいている状況ではないだろうか。その階層に留まっている人たちをどうやって上の階層に引き上げるかは、マネジメントがテーマ選定を意識しなければ、なかなか実現しないと考えられる。
研究発表5「経営から視座した品質工学推進の課題」((有)近岡技術経営研究所、近岡淳)
企業の数だけ経営方法に独自性はあるのだろうが、経営課題に対し、より効果を創出するための企業内における品質工学推進方法について、普遍的な方法があるのかを問い続けている。その1つとして、品質工学会において「経営における品質工学研究委員会」を組織し、経営層への品質工学普及を目的として議論をまとめた経緯がある。今回、品質工学を企業内の活動に導入している企業から推進方法と課題などを集めて整理することで、より有効な推進の方向性と課題を見出すことを狙いとした研究をおこなった。その目的は、(1)定着期に到達するための有効なマネジメントは何か、(2)経営課題に対して品質工学を有効に活用するための技術部門のしくみの改革はどうあるべきかを探ることである。
研究のためのデータは、品質工学を活用状況がさまざまな企業へのアンケートから抽出する。アンケート依頼企業34社中、回答企業28社の内訳は、定着期8社、発展期11社、導入期3社、停滞期6社であった。定着期までは最低10数年の期間が必要ということであった。アンケートより企業プロファイル、現在の推進状況、品質工学を効果的に推進するための工夫について67項目を抽出して数値化し、誤圧による解析を実施した。
単位空間として選定した企業は3社で、品質工学推進レベルが定着期であり、経営的成果も出し続けていて継続性も高い企業である。また項目の類似性もあり単位空間として妥当とした。
誤圧解析の結果、発展期の企業でも誤圧の距離の大きさから3つの群に層別された。T群は距離2.09と単位空間の企業に近く、「技術開発の機能性評価」に少し違いがある程度であった。U・V群の企業は項目診断のパターンは個々に違いがある。V群の企業は距離8〜9程度と単位空間の企業と乖離している。単位空間の企業と項目診断で違いがあるのは、教育における田口哲学の扱い、技術開発時の機能性評価、品質工学利用の文化醸成などであった。さらに経営的視点が揃っている企業14社のデータを活用し、再度類似した3社で単位空間を構成し誤圧解析を実施した。項目診断の結果、単位空間と違いがあるのは、発表会の頻度、品質工学への期待、技術開発・製品開発への生産性向上、業務フローへの組み込み、製品のロバスト性向上、発表会の規模、教育の田口哲学の扱いなどであった。
品質工学を継続して効果的に活用するためには、経営層の理解と技術経営の一環として品質工学の活用を位置づけることが肝要ということである。課題は、(1)品質工学の効用を経営層にどのように説明していくか、(2)品質工学の成果を経営層にもわかるようにどのような指標で数値化するか、(3)品質工学を開発フェーズのどのタイミングに適用すると効果的か、(4)品質工学を適用する具体的なテーマ選択をどのような視点でおこなうか、(5)技術部門のマネジャーや技術者に、効果的な実践の場の設定とその運用、さらに並行して田口哲学を伝える教育内容をどう構築するかということである。
今回の研究で、誤圧の距離が単位空間との違いを表しており、品質工学活用レベルをさらに発展させるための診断として有効である可能性が示された。項目診断により改善すべき項目も把握することができるが、品質工学推進の診断として使うレベルにするには、有効な項目のさらなる研究が必要である。質疑において近岡は「実際やってみるとアンケートそのものの難しさがわかった。結果を見てから気づくこともあり、メールだけでなくヒヤリングも必要ではないか」、「社内のことはわかるが、市場のことはよくわからない。長期のことをフィードバックしなくてはロバストの実力はわからない」と述べた。
アンケート解析は難しく、まだこれからの研究といえるが、誤圧解析で得られた結果がそれ程的外れとは思えない。研究発表4の「テーマ選択の三階層」にも至らない企業は、マネジメントをターゲットにした理解と普及に役立つ情報が欲しいので、この研究は役に立つはずである。項目診断で個別企業ごとの診断ができるレベルになるのが先か、各企業が自力でマネジメントに理解させることに成功するのが先かわからないが、有効な項目診断技術の確立が望まれる。
パネル討論「品質工学の果たすべき役割を探る」
研究発表者5名をパネリストとし、(一財)地域産学官連携ものづくり研究機構の久米原宏之による司会で、「品質工学の果たすべき役割を探る」というテーマでパネル討論がおこなわれた。久米原がパネル討論に際して用意した資料によると「立て続けに起きた想定が難しい自然界の現象からの防災対応などを予測技術と評価、実践の成果として確立していくことが、想定外を減少させるのに効果が期待される。また、人間が作り続けた多くのものからの社会損失低減に向けて人間の智慧から創出され具現化の証となるものづくりにあるべきであると考えられる」、「サブテーマ『マクロ視点からの戦略的評価基準の決定』の発表事例から討論を踏まえて、中身に関連した有機的なディスカッションが必要」とのことである。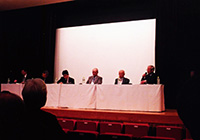
まず、現在の品質工学会におけるキーワードである「マクロ視点」について各発表者のコメントは、「能書きだけではいけない。自分の技術課題は何かを考えること。何を自分がしているかを言うこと(矢野宏)」、「計量研究所で設定した標準をいかに活用させるか。活用されなければ研究に意味がなくなる(中井功)」、「品質をコストで表現することがすごい。前回プリンタカートリッジというミクロなテーマに取り組んだので、それをもう少し大きくしたのが今回(曽我光英)」、「テーマの影響の大きさとしてのマクロ、微視的に見るマクロがあり、マクロに見ると汎用性が見えてくる。これまでで技展のフレームを作ってきたので、これからはパラメータを入れる段階。テーマ選択が重要なので、今回の発表に選んだ(吉澤正孝)」、「タイトルが大きすぎた。1980年代初めより品質工学を見てきた。いろいろうまくいったテーマも失敗したテーマも見てきたので、何が効いているかを調べたかった。アンケート解析にトライしたが難しい(近岡淳)」であった。
次にフロアから「生産現場のテーマを見ると不良の話が多い。また生産スピードを上げる必要がある。こういう観点からのテーマはどうか」という質問があり、吉澤が「原価かリードタイムかが常套手段。スピードを上げれば品質は落ちる。だから品質を上げる必要がある。社内の品質は原価問題。推進は言い出しっぺがやる。推進部隊はそのお手伝いに過ぎない」との回答をおこなった。
アンケートに関しては、「アンケート回答者が誰かで情報が変わってくる。テーマ選択の視点やどこまでマネジメント視点を考えているかはマネジャーしか書けない(近岡)」、「海外生産移行で品質工学を適用する人も減っている。サービス産業が増えているので、ここが新しい領域。マクロで整理すると新たなテーマが見えてくる(吉澤)」、「品質工学をわからせることの難しさがある。アンケートテーマにしても、誤圧、単位空間など本当は説明すべきだが、話をしていたら時間がなくなってしまう。これからは発表のしかたも考えなくてはならない(矢野)」と答えた。
しがらみに関して中井は、「しがらみへの打開策として、学会内から声が出なくてはならない。社会的損失を低減させることが必要」と話し、久米原より「学会発表が組織の一発表ではなく、学会から外に出るようなしくみが必要」と付け加えられた。
教育についての議論もあった。芝浦工大斎藤之男の「今の教育に何が欠けているから駄目だと思うか」との問いかけに、「機械学会では1970年代よりいわれていたこと、不完全な学生は企業で教育せざるを得ない。文科省は大学に補助金を出す制度があるが、たくさんの学生を入学させ、たくさんの学生を卒業させる必要がある。その結果、できの悪い学生がたくさん生まれる。そんな学生が企業に入るので企業の損失となり、ひいては日本の損失となる(矢野)」、「手法を教えるのみで、マクロ視点を教えていない(中井)」、「自分の周りの若いエンジニアはむしろ粒ぞろいに思う(曽我)」と答えた。吉澤は「単に問題を解くのではなく、疑問を持つ「問い題」をすることが大切。自分で知識を獲得する人が求められる」と語り、呼応して久米原は「日本はHow to、海外はWhyから始まる」と言い、近岡は「1976年頃、まだ知識教育でHow toもWhyもなかった。R&D、進め方など場の設定を先生には考えてほしい。優秀な学生は自分から先生に取りつく」と要望した。最初に問いかけをした斎藤からは「品質工学のフィロソフィで教育カリキュラムを直したい」とコメントがあった。半導体権威の東北大大見忠弘は「教員の採点システムのスコアを上げるために学生に迎合する教授を叩きのめす。導入されている採点システムも活用されていない。自分のために怒鳴りつけると理解している学生は自分に良い評価をしてくれる。半導体プロセスも結果に影響を与えるパラメータをきちんと制御すれば、検査は不要だと1980年代から主張してきた。しかし、今はどこでも全数検査をしている。このような無駄を止めさせたい」と発言した。
パネル討論のタイトルは1つであるし、本大会のテーマも1つであるが、個々の研究内容が多岐にわたっている。パネル討論を通してそれらの共通性を見出す行為は、一見ベクトルの向きが違うかのような研究について合成ベクトルを求め、ベクトルの意味するところを会場で共有しようというのであるから、とても難しいと感じる。
今回の個々の研究発表のキーワード(太字)を、本記事冒頭RQES2013まとめのキーワード(カギ括弧)との関連を筆者なりにまとめる。技術開発におけるマネジメントは「適切なテーマ選定の指針」のもと、その「ゴール設定」のなかに成果の活用を明確化することが求められる。またマネジメントにおいて「プロジェクトを横断的に見る」ことで関係者および関係組織への働きかけがしっかりおこなわれており、個々の技術者が自立し力を発揮することで、マネジメントと技術者が「有機的に作用」することが望ましい。また、その両者に必要なものは将来を予測する能力である。
招待講演「YKKにおける技術強化」(YKK(株)取締役副社長、大谷渡)
読者の皆さんが身に着けているものに1つくらいは付いているものがファスナーである。ファスナーを確認すればYKK製である可能性が高い。なぜならYKKファスナーの世界シェアは6割にもなるというからである。ファスニング事業、AP(建材)事業の2つの事業とそれを支える工機技術部を持ち、世界71カ国で事業を展開するグローバル企業である。各事業部を縦串にし、6極の地域統括体制を横串にした管理体制を取っている。YKK創業者の吉田忠雄の企業精神である、他人の利益を図らずして自らの反映はないという意味の「善の巡環」をYKKグループの基本姿勢としている。「一度出した工場は役割を変えてでも地域の利益のために残す」にその姿勢が表れている。
工機部門は商品に使う材料開発、金型材料開発、加工技術開発、設備・ライン開発、機械・金型製造を自社でおこなうことを基本としている。これを「一貫生産思想」と呼び、時代が変わっても、強化・継続しており、これがYKKの強さである。自社ですべておこなうので、世界中で同じ品質のものづくりができる。また、設備が自前なので、投資をすれば社内で環流する。最近は外注する部分もあるが、評価はYKK自らがおこない、技術を他人に任せない姿勢を貫いている。事業を集中しているため、ファスナー専用機械および窓専用ラインの改善・改良・進化に限定した技術開発をしている。ファスナーと建材以外は研究開発成果が出せなくて止めさせた経緯がある。
大谷が工機技術本部長に就任し、開発の方向転換として、技術開発の領域をファスニング事業・AP事業に限定した。技術として立派でも、事業に役に立たなければ意味がないと言う。また、実践と原理原則の割合を50:50にするため、実践に強い設備開発機能と原理原則に強い研究開発機能を統合した。開発方針を「高速・自動化」から「使いやすさ・安定性」に転換。高速・自動化が新興国では逆に使いにくいという考えによるものである。製造面は生産性より「リードタイム短縮」をめざすようにした。YKKでは「生産性」は禁句としている。また、中長期視点での技術開発として、材料・プロセス開発、分析・解析の評価技術を重視している。開発の方向転換にともなう社員の考え方を変えるのに数年かかったようである。経営企画畑出身の文系経営者の大谷によれば、良くも悪くも技術者は信じたものに固執する人種ということである。YKKのイノベーションは、技術の継続的な改善・改良・進化を指し、目先の課題をやり残して進化をしないということである。
YKKでは日本国内で競争力を維持・強化できる生産体制の構築のため、2016年に新工場を建設する。新工場建設にともない、作業面積、物流距離、設備台数、製造人員を大幅に減らす。精密部品の安定生産と社員の働きやすさを両立した工場をめざし、「窓のある精密機械工場」への挑戦を掲げている。竹中工務店によると、窓のある工場は生産性5%向上、うつ病のリスク低減効果という論文調査結果がある。精密機械にとって窓の存在はリスクがあるが、社員のためと考えている。また、課題を与え社員に考えてやらせるためでもある。床面積削減と社員の移動歩数、時間を金額換算し、マーキングして原価をはじきだしたら、社員が率先して取り組むようになった。
品質工学導入として、3年前より矢野に指導を仰ぐようになった。最初は反対もあったそうである。技術も経営も基本は同じ原理原則を大切にするということである。技術の本質以外で改善しようとしてもうまくいかない。その部分は品質工学とマッチしている。
「他国が真似するのが普通であるが、ファスナーはどうか」という質問に対し、大谷は「中国にはファスナー会社が200社ある。YKKは専用機、材料、熱処理など何でも内製して一貫生産しているのが強み。簡単には突き崩せない。設備の処分も外ではしない。家電メーカーは外製でやっている。しかし外のメーカーは複数の会社から仕事を受けないと経営できない。秘密保持契約を結んでいても、設計思想は設備に反映されてしまう。そうすると他社の設備に設計思想が反映され、結果として外に漏れてしまう。あと、アパレル業界はどんどん世界を回るが、それにYKKの設備がついていける」と自信を見せた。
次に「品質工学への期待で、真の技術者育成とある。品質工学のどういう点に着目したか」という質問に対し、大谷は「工機部門の実践は強かったが、原理原則が弱かったので高めていった。原理原則が強すぎると実践できない研究開発になる。実践と原理原則の割合を50:50にしたい。品質工学はそのバランスが30:70くらいでないかと思う。品質工学を取り入れて、50:50の工機部門になって欲しい」と述べた。
また「80年思想が継続している」秘訣については、「技術者はアプローチが技術から入ってしまう。マーケットを調査させ、目的をはっきりさせる。顧客が価値を認めてくれるか考えて開発させる。技術は経営全部につながっている」と述べた。
YKKは今まで技術を表立って公開しない会社だと聞いている。そんな会社が去る6月に開催された品質工学研究発表大会では7件もの研究発表をした。このことは品質工学が汎用的な評価技術であり、発表をしても研究対象の技術詳細が分からないということを示している。独自の経営の哲学を持っているYKKが汎用的な技術の哲学を導入した結果、パラメータ設計と実践と原理原則のバランス改善の相乗効果で、工機部門の技術開発の質が向上したという講演を聴けることを望む。 |